ABOUT US
At Lamb Precision Engineering Ltd we pride ourselves on being at the forefront of CNC machining technology, delivering quality and precision to meet your every need. With a promise of innovation, expertise, and customer satisfaction, we are your trusted partner for all your machining requirements. With a steadfast commitment to precision and excellence, we specialise in 3 and 4-axis CNC milling, CNC turning, and fabrication services.
​
Lamb Engineering was founded in 1988 by Larry Houghton and the company has continued to flourish and develop to where it is today. New owners, Jordan Hicks and Finley Parsons, continue the evolution of the business, introducing exciting new methods and technology to adapt to an ever-changing industry, but all the while maintaining a firm commitment to their existing customers.
​
Whether you're looking for precision prototypes, custom parts, or small to medium scale production, Lamb Engineering is here to bring your vision to life. Explore our range of services and discover why Lamb Engineering is your go-to destination for CNC machining solutions.
​
Our team of experienced professionals are dedicated to our craftsmanship and innovation. We take pride in our ability to tackle complex projects so whether you require intricate milling, precise turning or expert fabrication, we have the expertise and resources to deliver outstanding results, every time.
​
Customer satisfaction is at the forefront of everything we do. We work closely with our clients to understand their unique needs and specifications and deliver tailored solutions that meet their exact requirements.
When you choose Lamb Engineering, you can trust that your project is in capable hands.
Experience the difference with our unparalleled CNC machining services.
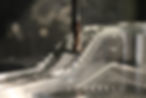
MACHINERY
Lamb Engineering has an extensive range of equipment on-site, making us the perfect partner for all your machining requirements.
Explore our range of machinery below.

5 x XYZ Mini Mills (CNC)
3-axis CNC mills are the cornerstone of precision machining, offering unparalleled versatility and accuracy for a wide range of applications. With their ability to move along the X, Y, and Z axes, these machines excel at creating intricate shapes, contours, and surfaces with utmost precision. From crafting prototypes to producing complex 3D components, 3-axis CNC mills provide the flexibility and reliability needed to meet the demands of modern manufacturing. Equipped with advanced control systems and robust construction, these mills deliver consistent and high-quality results, making them indispensable tools in any workshop or production facility. Whether you're working with metals, plastics, or composites, 3-axis CNC mills empower you to unleash your creativity and bring your ideas to life with unmatched precision and efficiency.

2 x XYZ Full CNC Lathes
CNC lathes stand as the pinnacle of precision and efficiency in the realm of machining. These sophisticated machines revolutionise the turning process by automating the shaping of materials with unparalleled accuracy. Equipped with computer-controlled systems, CNC lathes enable precise control over rotation speeds, cutting depths, and tool movements, resulting in flawless finishes and tight tolerances. Whether crafting one off intricate components or producing high-volume parts, CNC lathes excel in versatility and reliability. With their ability to work with a variety of materials, from metals to plastics, CNC lathes cater to a wide range of industries and applications. From simple cylindrical shapes to complex contours, these machines empower manufacturers to achieve consistent results with efficiency and precision, setting new standards in modern machining practices.
4 x Manual Centre Lathes
Manual lathes have long been a cornerstone of traditional machining, embodying craftsmanship and versatility in the workshop. These machines operated by skilled machinists, offer precise control over turning operations, allowing for the creation of intricate cylindrical shapes and contours from raw materials. With manual lathes, operators utilise hand wheels and levers to manipulate cutting tools, tailoring each cut to exact specifications. While manual lathes lack the automation of their CNC counterparts, they provide a tactile connection between machinist and work piece, fostering a deep understanding of the machining process. This hands-on approach not only cultivates craftsmanship but also enables machinists to tackle a wide range of tasks, from simple repairs to complex custom fabrication. Manual lathes remain indispensable in workshops worldwide, embodying a timeless blend of tradition, skill, and precision in the art of machining.

2 x Manual Milling Machines
Manual mills, stalwarts of traditional machining, are renowned for their versatility and precision in shaping raw materials into intricate components. Operated by skilled machinists, manual mills provide a hands-on approach to milling operations, allowing for meticulous control over the cutting process. Machinists manipulate hand cranks, wheels, and levers to guide the cutting tool across the work piece, adjusting parameters with precision to achieve desired outcomes. Despite the absence of automation found in CNC mills, manual mills offer a unique level of craftsmanship and customisation, fostering a deep understanding of machining principles. This intimate connection between operator and machine not only hones skills but also enables machinists to tackle a wide array of tasks, from basic repairs to complex fabrication projects. Manual mills remain indispensable in workshops worldwide, embodying a timeless tradition of skill, ingenuity, and precision in the art of machining.


1 x 27-inch Surface Grinder
Surface grinders are fundamental machines in the realm of precision grinding, renowned for their ability to achieve flat and smooth surfaces with exceptional accuracy. These machines utilise a rotating grinding wheel to remove material from the surface of a work piece, ensuring uniformity and precision to within microns. Surface grinders excel in producing precise finishes on flat or contoured surfaces, making them indispensable tools in industries ranging from automotive to aerospace. Operators can adjust parameters such as speed, depth of cut, and feed rate to tailor the grinding process to specific requirements. Whether removing imperfections from metal parts or refining the surface of intricate components, surface grinders deliver consistent results, meeting the most demanding tolerances with ease. With their precision, versatility, and reliability, surface grinders play a vital role in achieving the highest standards of quality and performance in modern manufacturing processes.

TIG and MIG Welding Facilities
TIG (Tungsten Inert Gas) and MIG (Metal Inert Gas) welding are two of the most widely used techniques in the field of metal fabrication, each offering distinct advantages and applications. TIG welding involves the use of a non-consumable tungsten electrode to create an electric arc, which melts the base metal and filler rod, if necessary, to form a weld pool. The weld area is shielded from atmospheric contamination by an inert gas, typically argon, resulting in high-quality, precise welds suitable for thin materials and critical applications like aerospace and nuclear industries. On the other hand, MIG welding utilises a continuously fed consumable wire electrode and a shielding gas, typically a mixture of argon and carbon dioxide, to create an electric arc between the electrode and the work piece. MIG welding is known for its speed and efficiency, making it ideal for high-volume production and welding thicker materials, such as structural steel and automotive components. Both TIG and MIG welding techniques offer versatility, reliability, and strength, playing indispensable roles in various industries and applications, from automotive manufacturing to construction, and beyond.
1 x 4th Axis
The addition of 4th axis capabilities takes your machining abilities to new heights, tackling complex geometries, multi-sided machining, and intricate designs with ease. Whether you're creating prototypes, molds, or intricate components, our CNC mills empower you to bring your ideas to life with unparalleled versatility.

Inspection
Machinist inspection is a critical aspect of manufacturing processes, ensuring the precision, quality, and functionality of machined components. Our machinist inspectors meticulously examine finished products, utilising a variety of measurement tools such as calipers, micrometres, gauges, shadow graphs and roughness tester. Our keen attention to detail allows us to detect even the slightest deviations from specifications, guaranteeing that each piece meets the required standards for accuracy and performance. Beyond measurements, our machinist inspectors assess surface finish, tolerances, and overall integrity, employing both visual inspection and advanced techniques like non-destructive testing when necessary. Their role is pivotal in maintaining quality control throughout the production process, ultimately contributing to the reliability and safety of the final products.
